Newsroom
Newsroom
Latest News
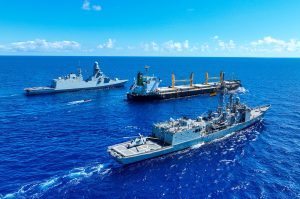
April 15, 2024
ScanEagle Deployed on The Frigate Canarias Assists in the Liberation of a Ship Kidnapped by Pirates in Somali Waters
Operation EUNAVFOR ATALANTA confirms the release of the ship ABDULLAH and its 23 crew members.
Read More
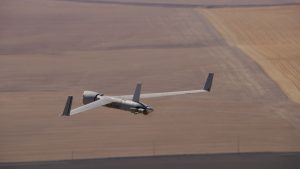
April 11, 2024
Insitu Awarded $84M IDIQ Contract Modification by NAVAIR for ScanEagle and RQ-21A UAS
Insitu Awarded $84M IDIQ Contract Modification by NAVAIR for ScanEagle and RQ-21A UAS April 11,…
Read More
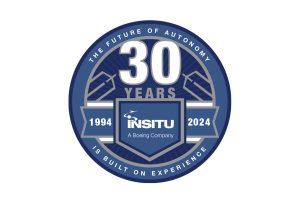
April 08, 2024
Insitu Celebrates 30 Years of Uncrewed Aircraft Innovation Excellence at Sea-Air-Space
Insitu Celebrates 30 Years of Uncrewed Aircraft Innovation Excellence at Sea-Air-Space BINGEN, Wash., April 8,…
Read More
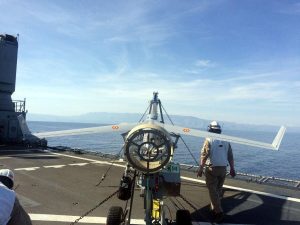
December 19, 2023
ScanEagle Assists in Response to Hijack of M/V Ruen
ScanEagle Assists in Response to Hijack of M/V Ruen Original story from EUNAVFOR. DEVELOPMENT OF…
Read More
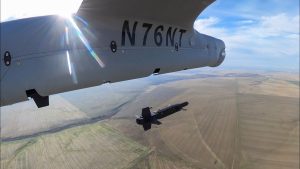
December 12, 2023
Insitu Announces Successful Shryke Demonstration with Integrator Uncrewed Aircraft System
Insitu Announces Successful Shryke Demonstration with Integrator Uncrewed Aircraft System BINGEN, Wash., Dec. 12, 2023…
Read More
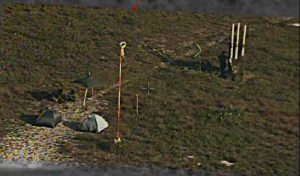
December 07, 2023
QE-1 Squadron employs the ScanEagle in support of Special Operations
On November 22, the 1st Remotely Piloted Aircraft Squadron (QE-1) carried out a Surveillance and…
Read More
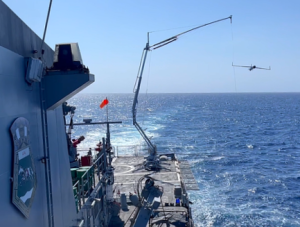
December 06, 2023
QE-1 Squadron carries out ScanEagle’s first embarked operation at NPaOc ‘Apa’
On November 21, the 1st Remotely Piloted Aircraft Squadron (QE-1) carried out, for the first…
Read More
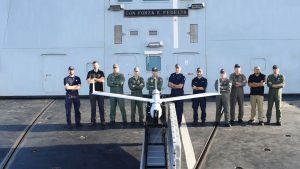
November 13, 2023
The Scaneagle project takes off from the flight deck of the Bergamini ship
The Scaneagle project takes off from the flight deck of the Bergamini ship November 13,…
Read More
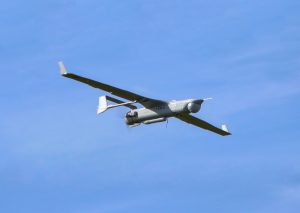
November 08, 2023
Insitu Announces AI-Powered, Wide-Area Maritime Search Capability for Integrator UAS in Collaboration with Overwatch Imaging
Insitu Announces AI-Powered, Wide-Area Maritime Search Capability for Integrator UAS in Collaboration with Overwatch Imaging…
Read More
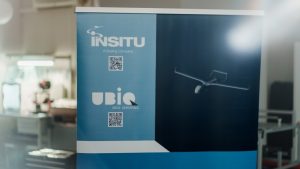
October 26, 2023
UBIQ Aerospace and Boeing Insitu Establish Visionary Partnership to Redefine Cold Climate Aircraft Technology
UBIQ Aerospace and Boeing Insitu Establish Visionary Partnership to Redefine Cold Climate Aircraft Technology Trondheim,…
Read More
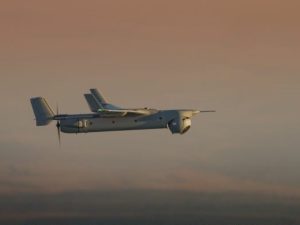
October 17, 2023
Insitu and Innovaero to develop unmanned aerial attack systems
Insitu and Innovaero to develop unmanned aerial attack systems Read the original article at AUManufacturing.…
Read More
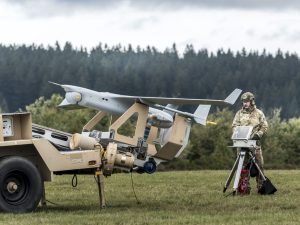
October 08, 2023
Belgian Defence Gets a Boost With US X-300 Integrator Drone Inaugural Flight
Belgian Defence Gets a Boost With US X-300 Integrator Drone Inaugural Flight Original article at…
Read More
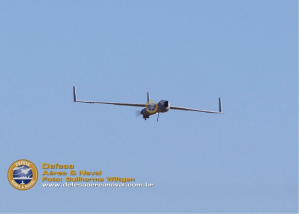
October 05, 2023
Tropicalex 2023: First operational use of the RQ-1 ScanEagle by the Brazilian Navy
Tropicalex 2023: First operational use of the RQ-1 ScanEagle by the Brazilian Navy By Guilherme…
Read More
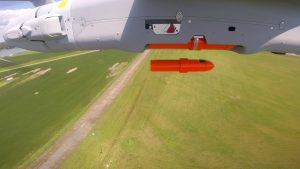
September 11, 2023
Insitu experimenting with armed Integrator UAVs
Insitu experimenting with armed Integrator UAVs 11 SEPTEMBER 2023 by Zach Rosenberg Read the full…
Read More
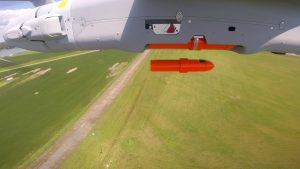
September 05, 2023
Insitu Announces Kinetic Capability for the Integrator Uncrewed Aircraft System (UAS)
Insitu, A Boeing Company, announced a munitions program for its Integrator UAS, which adds a…
Read More
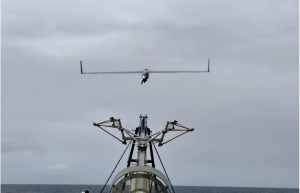
September 03, 2023
Scaneagle, the Navy drone that patrols the waters of the Indian Ocean in search of pirates
Scaneagle, the Navy drone that patrols the waters of the Indian Ocean in search of…
Read More
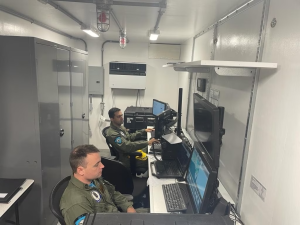
August 02, 2023
On the Coast of Rio, Navy RQ-1 ScanEagle Aircraft Participated in Search and Rescue Operation
On the Coast of Rio, Navy RQ-1 ScanEagle Aircraft Participated in Search and Rescue Operation…
Read More
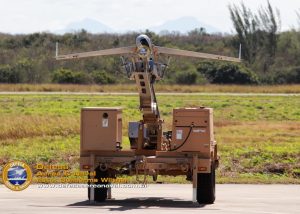
July 05, 2023
QE-1 Squadron Completes 1 Year of Service
QE-1 Squadron Completes 1 Year of Service Original story (in Portuguese) at Defesa Aéria &…
Read More
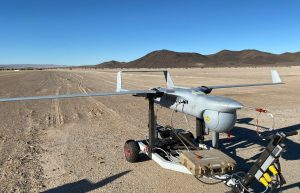
June 21, 2023
Insitu Pacific’s Uncrewed Next-gen Sensors Demonstrated at U.S. Army Exercise
Insitu Pacific demonstrated next generation sensor capabilities and autonomous technologies in California as part of…
Read More
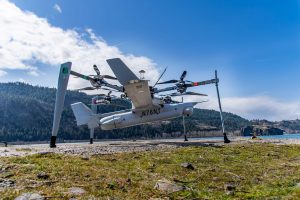
April 03, 2023
Insitu Announces its High Seas, Long Endurance Integrator VTOL Uncrewed Aircraft System at Navy League’s Sea-Air-Space Global Maritime Expo
Insitu Announces its High Seas, Long Endurance Integrator VTOL Uncrewed Aircraft System at Navy League’s…
Read More
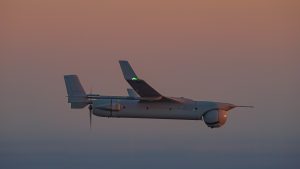
March 30, 2023
Insitu Sets Company Record for Longest Flight at 25.5 hours with its Integrator Uncrewed Aircraft System
Insitu Sets Company Record for Longest Flight at 25.5 hours with its Integrator Uncrewed Aircraft System…
Read More
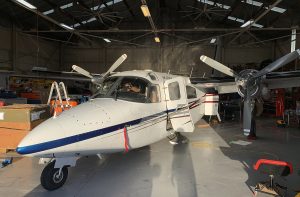
December 08, 2022
Boeing, Insitu and Courtney Aviation Test 4G LTE Technology to Improve Remote Data Connectivity
Courtney Aviations’ Aerocommander with networking equipment, microwave downlink and cellular eNodeB installed. Photo: Insitu Boeing,…
Read More
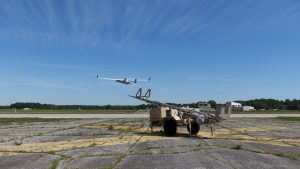
August 08, 2022
Manned/Unmanned teaming made safer with Naval Aviation’s new avoidance tech
Manned/Unmanned teaming made safer with Naval Aviation’s new avoidance tech Aug 8, 2022 – NAVAIR…
Read More
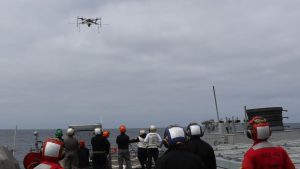
July 27, 2022
U.S. Navy holds UAS wide-area mission demonstration
U.S. Navy holds UAS wide-area mission demonstration Jul 27, 2022 – NAVAIR News Naval Air…
Read More
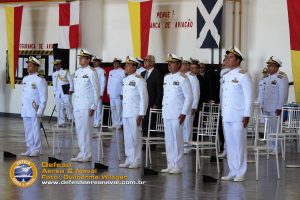
July 10, 2022
Brazilian Navy activates its first Squadron of Remotely Piloted Aircraft
Brazilian Navy activates its first Squadron of Remotely Piloted Aircraft Translated from Portuguese – Original…
Read More
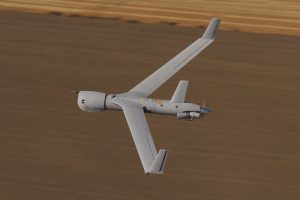
July 02, 2022
Brazilian Navy makes first ScanEagle drone launch
Brazilian Navy makes first ScanEagle drone launch Remotely piloted aircraft will be used in reconnaissance,…
Read More
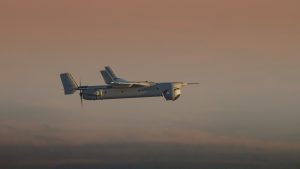
June 23, 2022
NAVFAC Completes Construction Of Royal Thai Navy Facility In 100 Days
NAVFAC Completes Construction Of Royal Thai Navy Facility In 100 Days Thailand, 23 June 2022…
Read More
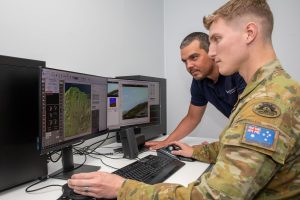
June 23, 2022
Australian Army commences training on Integrator UAS
Australian Army commences training on Integrator UAS Boeing subsidiary Insitu Pacific has announced it has…
Read More
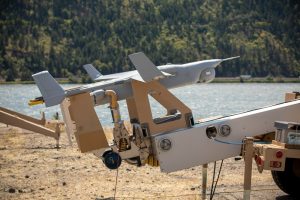
June 14, 2022
The Australian Army will receive two dozen Integrator UAVs sourced from Australia
The Australian Army will receive two dozen Integrator UAVs, with 80% of their systems’ content…
Read More
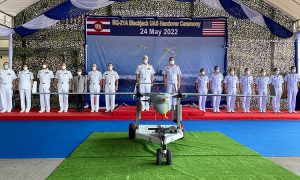
May 24, 2022
U.S. Navy Hands Over UAS to the Royal Thai Navy
U.S. Navy Formally Hands Over Unmanned Aircraft System to the Royal Thai Navy GULF OF…
Read More
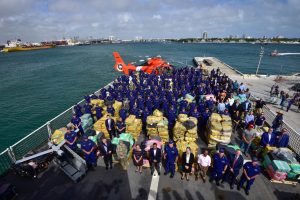
February 17, 2022
Insitu’s ScanEagle contributes to large US Coast Guard drug bust
The Coast Guard Cutter James’ (WMSL 754) crew offloaded approximately 54,500 pounds of cocaine and…
Read More
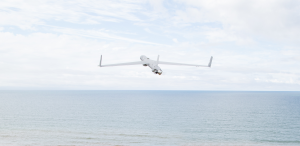
December 06, 2021
Royal Australian Navy Awards ScanEagle Contract Extension to Insitu Pacific
Royal Australian Navy Awards ScanEagleContract Extension to Insitu Pacific BRISBANE, Australia, December 6, 2020 –…
Read More
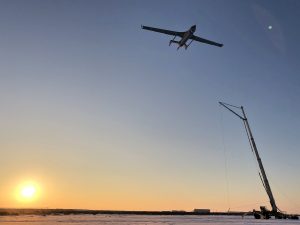
October 28, 2021
UBIQ Aerospace and Insitu join forces to “winterize” the Integrator UAS
UBIQ Aerospace and Insitu join forces to “winterize” the Integrator UAS UBIQ Aerospace of Trondheim,…
Read More
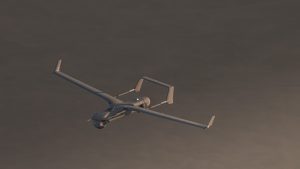
October 05, 2021
Insitu, GKN Aerospace and TNO Team Up to Develop Advanced Radar System for Integrator
Insitu, GKN Aerospace and TNO Team Up to Develop Advanced Radar System for Integrator UAS…
Read More
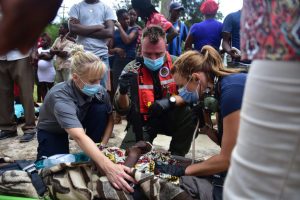
August 17, 2021
Navy, Coast Guard Units Rush to Aid Haitian Earthquake Victims
Navy, Coast Guard Units Rush to Aid Haitian Earthquake Victims ARLINGTON, Va. — Under the…
Read More
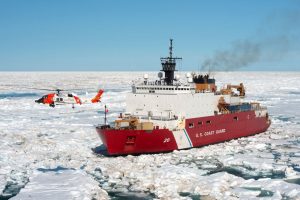
June 08, 2021
Insitu, Two Norwegian Companies Join Forces to Advance the Unmanned Aviation Ecosystem in the Arctic and High North
Insitu, Two Norwegian Companies Join Forces to Advance the Unmanned Aviation Ecosystem in the Arctic…
Read More
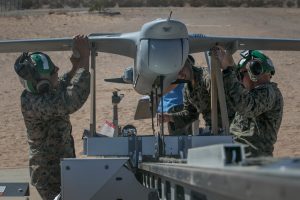
March 31, 2021
NAVSUP WSS supports achievement of 100% readiness rate
NAVSUP WSS Supports Achievement of 100% Readiness Rate By Lt. Cmdr. Chase Vizzier, NAVSUP WSS…
Read More
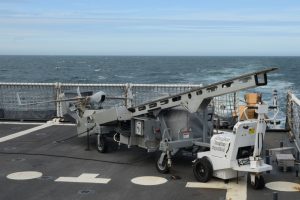
March 28, 2021
The ScanEagle And Blackjack UASs Will Reshape Maritime Surveillance
The ScanEagle And Blackjack UASs Will Reshape Maritime Surveillance Equipping surface ships with small unmanned…
Read More
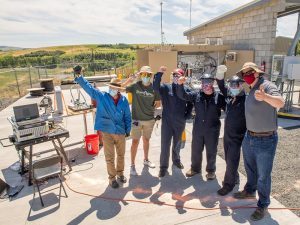
March 15, 2021
Insitu Advances its Fuel Cell Strategy
Insitu Advances its Fuel Cell Strategy BINGEN, Wash., March 15, 2021 – Insitu, a wholly-owned…
Read More

February 25, 2021
Cutter Kimball Conducts Patrol to Increase Maritime Presence
Cutter Kimball Conducts Patrol to Increase Maritime Presence and Support in Pacific HONOLULU — The…
Read More
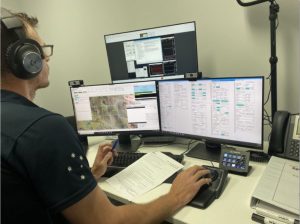
January 20, 2021
IPL launches virtual classroom for Defence
Insitu Pacific launches virtual classroom for Defence Brisbane, Australia – January 20, 2021 – The first…
Read More
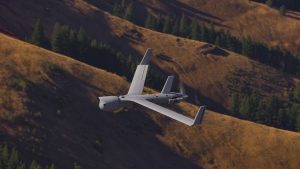
January 11, 2021
Insitu completes ScanEagle installation on USCG national security cutters
Insitu completes ScanEagle installation on USCG national security cutters Insitu has finished installing its ScanEagle…
Read More
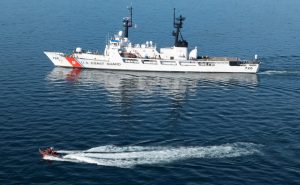
January 06, 2021
New U.S. Maritime Strategy Makes Case for More Coast Guard Cutters
New U.S. Maritime Strategy Makes Case for More Coast Guard Cutters The Coast Guard is…
Read More
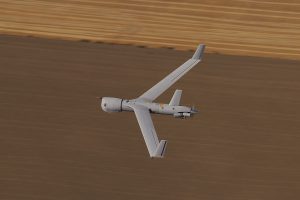
December 15, 2020
The Colombian Navy Deploys its ScanEagle against the Clan del Golfo
The Colombian Navy Deploys its ScanEagle against the Clan del Golfo In development of Operation…
Read More
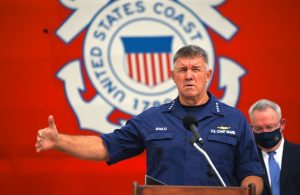
December 04, 2020
Schultz: Upcoming Coast Guard Budget Has ‘Dollars For People’ Focus
Schultz: Upcoming Coast Guard Budget Has ‘Dollars For People’ Focus Likewise, Ecuador, through U.S. Southern…
Read More
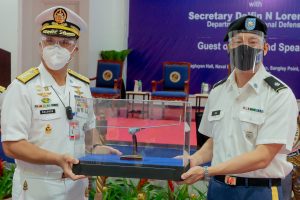
November 25, 2020
US delivers unmanned aerial system to Philippine Navy
US delivers unmanned aerial system to Philippine Navy MANILA, Philippines — The United States turned…
Read More
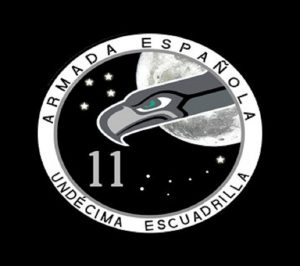
October 24, 2020
Spanish Navy’s ScanEagle Flies Over the Mediterranean From the Reina Sofia Frigate
Spanish Navy’s ScanEagle Flies Over the Mediterranean From the Reina Sofia Frigate The 11th Squadron…
Read More
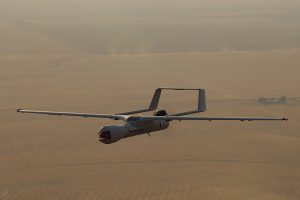
October 21, 2020
The UAV Advantage for Critical National Infrastructure
The UAV Advantage for Critical National Infrastructure The complex geopolitical environment in the Gulf demands…
Read More
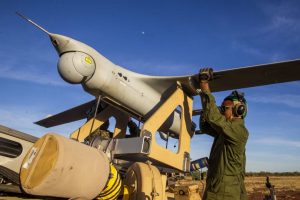
October 20, 2020
US Marines in remote corner of Australia are practicing to guide Air Force bombers to targets across the Pacific
US Marines in remote corner of Australia are practicing to guide Air Force bombers to…
Read More
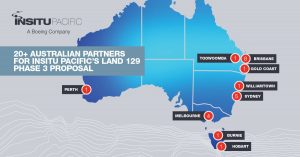
October 15, 2020
Insitu Pacific names strong Australian team for LAND 129
Insitu Pacific names strong Australian team to deliver growth and sustainability expertise for LAND 129…
Read More
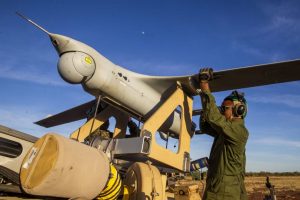
September 09, 2020
Navy Looking at Upgrades to RQ-21 UAS
Navy Looking at Upgrades to RQ-21 UAS Rear Adm. Brian Corey, program executive officer – Unmanned…
Read More
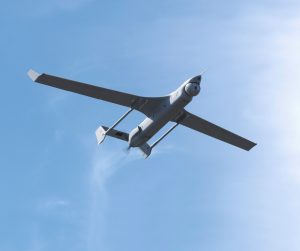
August 26, 2020
IPL, Nova Systems team up for Australian-led LAND 129 solution
Insitu Pacific, Nova Systems team up for Australian-led LAND 129 solution BRISBANE, Australia, August 26,…
Read More
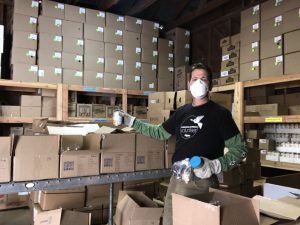
August 11, 2020
Standing Strong Together
Standing Stronger Together For The Gorge Insitu is honored to be working with organizations in…
Read More
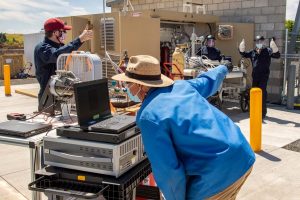
August 03, 2020
Successful Liquid Hydrogen Fuel Cell Test
Successful Liquid Hydrogen Fuel Cell Test August 3, 2020: Insitu together with a research team…
Read More
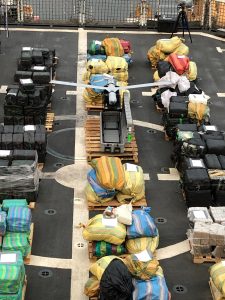
June 09, 2020
Insitu Expands Support of USCG Counter-narcotics Operations
Insitu Expands Support of USCG Counter-narcotics Operations BINGEN, Wash., June 9, 2020 – Building on a…
Read More
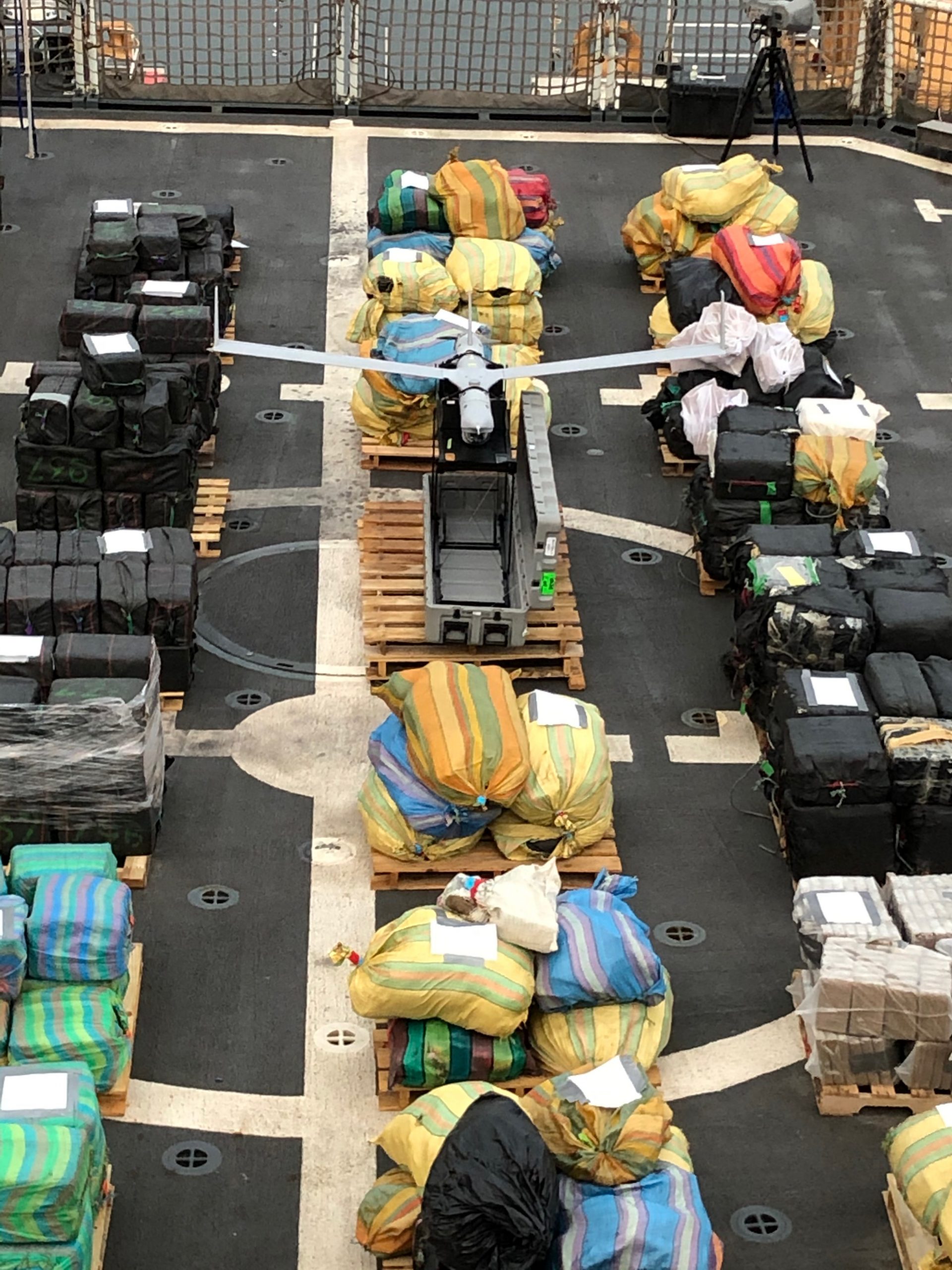
News
Insitu Expands Support of USCG Counter-narcotics Operations
Insitu ScanEagle has been deployed with US Coast Guard since 2017 supporting vital counter-narcotics effort with critical intelligence, surveillance and reconnaissance capabilities. To date, the system has played an integral role in preventing nearly $4 billion in illegal drugs reaching US shores.
Read More
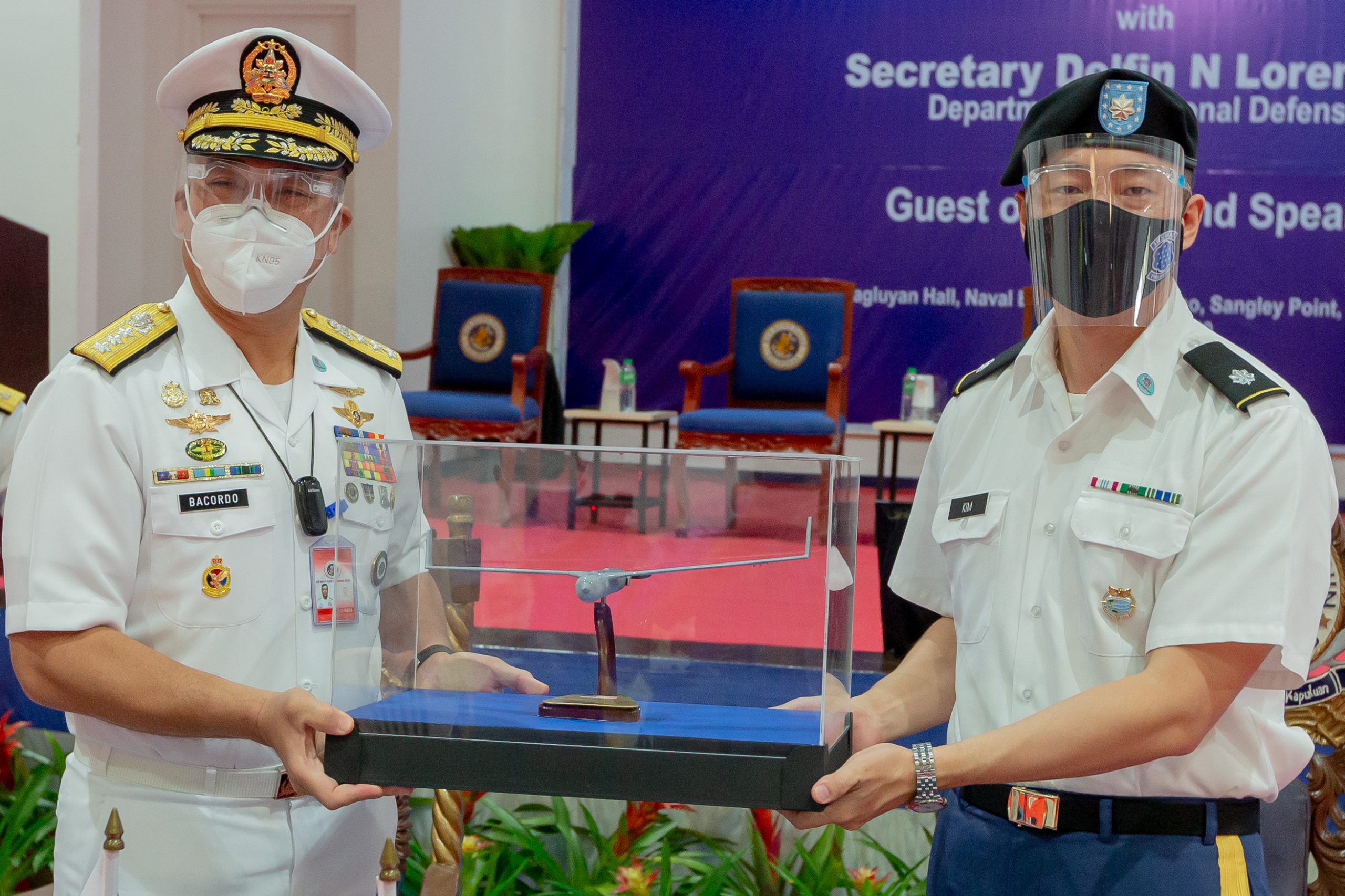
News
US delivers unmanned aerial system to Philippine Navy
US delivers unmanned aerial system to Philippine Navy
Read More
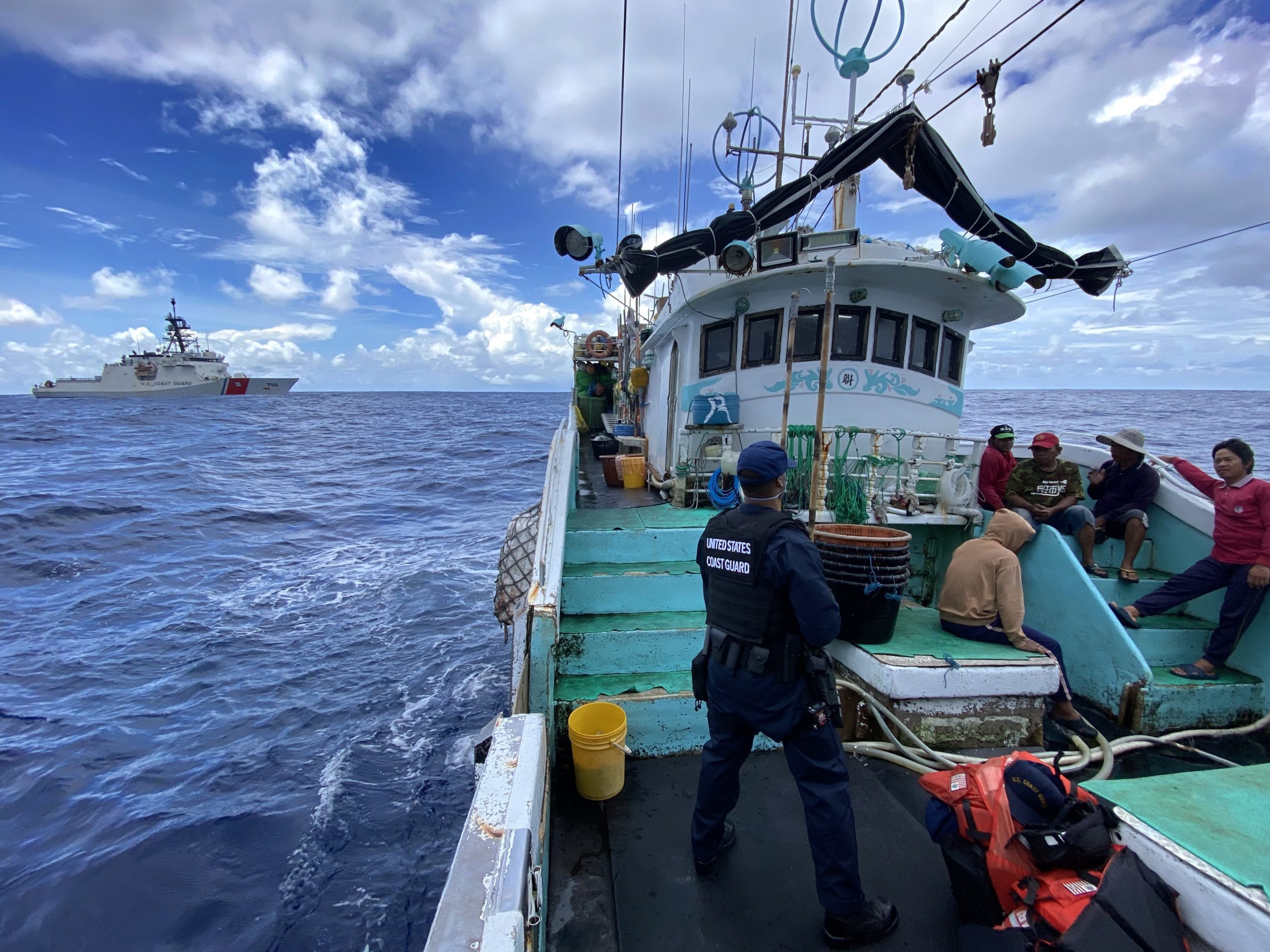
News
Cutter Kimball Conducts Patrol to Increase Maritime Presence
Honolulu, HI –
The use of SUAS expands maritime domain awareness and provides persistent airborne surveillance on maritime hazards, threats, and rescue operations.
Read More